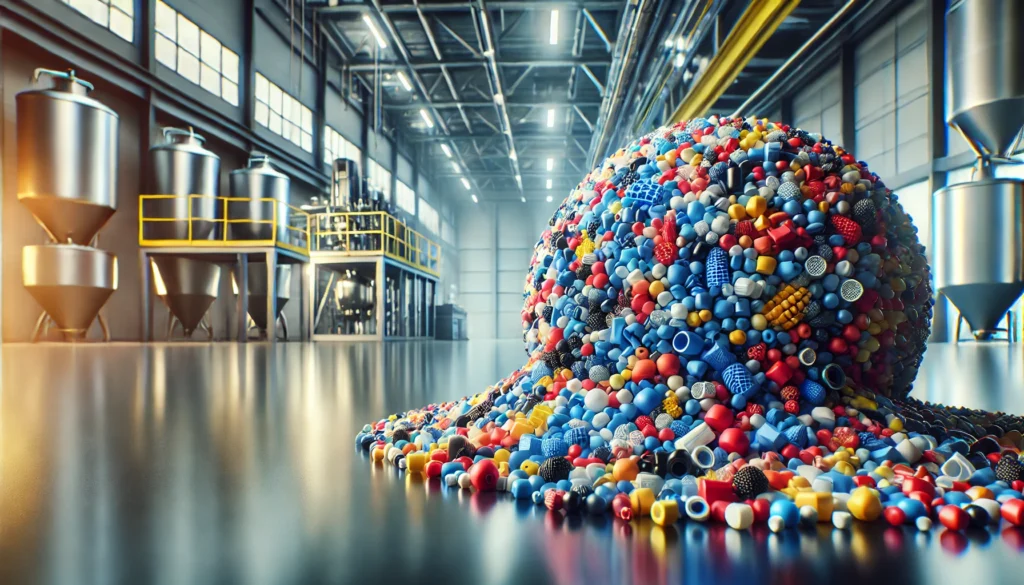
What is Masterbatch?
Masterbatch is a concentrated, polymer-based material made by combining various colors and additives into a polymer carrier. This material is produced during a thermal process and high shear extrusion. After cooling, the masterbatch is directed into a pelletizer and turned into small granules. It allows plastic processors to economically and cost-effectively add coloring to plastics during the manufacturing process.
In this article, we will explore the concept of masterbatch, its features, various types, and its wide applications in the plastics industry.
Definition of Masterbatch
Masterbatch, also known as color concentrate in the plastic industry, is a granule used for coloring thermoplastics. This material consists of one or more pigments and a resin carrier specific to the polymer. The main feature of masterbatch is that it enables processors to easily and cost-effectively add the desired color to various polymers.
During the production of masterbatch, pigments and additives are combined into a polymer carrier to create a uniform and high-quality mixture. This mixing and blending occur at high temperatures to ensure that the materials bond well and form a stable compound.
Features of Masterbatch
Masterbatch has unique characteristics that make it highly suitable for use in various industries. Some of the key features of this material include:
- Uniform Coloring: Masterbatch ensures uniform and high-quality coloring due to the precise blending of pigments and resin carrier.
- Cost-effectiveness: Using masterbatch helps plastic producers lower the cost of coloring their products. Compared to other methods, such as using liquid dyes, it is more economical.
- High Variety: Masterbatch is produced in various types, making it possible to produce a wide range of colors and shades. This provides great flexibility in producing diverse products.
- Chemical Resistance: Masterbatch is resistant to various chemicals, making it suitable for industries like food and pharmaceuticals.
- Preserving Physical Properties: After being added to plastics, masterbatch does not affect the physical properties of the polymer, ensuring that characteristics such as strength and flexibility are maintained.
Types of Masterbatch
Masterbatches are generally classified into two categories: color masterbatches and additive masterbatches.
- Color Masterbatches: These are specifically used to color thermoplastics. Color masterbatches are made from natural or synthetic pigments and can evenly distribute the pigment during the production of plastic products.
- Additive Masterbatches: These masterbatches are used to impart specific properties to plastics. These properties can include UV resistance, antibacterial characteristics, heat resistance, or even antistatic properties. Additive masterbatches are commonly used in industries such as automotive and packaging.
Masterbatch Production Process
The production process of masterbatch generally follows these steps:
- Selecting Raw Materials: First, raw materials such as pigments, additives, and the resin carrier are chosen. These materials must be carefully selected to ensure the desired properties are achieved in the final masterbatch.
- Mixing and Polymerization: The raw materials are blended at high temperatures using special extruders. During this stage, the coloring material is evenly distributed within the polymer carrier.
- Shaping: After mixing and polymerization, the mixture is transformed into small granules or pellets, which can then be used easily in the plastic production process.
- Quality Control: At the end of the process, the produced masterbatch must undergo quality checks to ensure color and additive uniformity. These checks may include physical, chemical, and color tests.
Applications of Masterbatch
Masterbatch is used in various industries, offering numerous advantages for plastic manufacturers and processors. Some of its applications include:
- Plastic and Packaging Industry: Masterbatch is widely used in the plastic industry to produce various colored and transparent plastics. It is also used in the packaging of food and pharmaceuticals to add colors and specific properties to packaging materials.
- Automotive Industry: Masterbatches are used in producing plastic components for vehicles, such as dashboards, bumpers, and interior parts. It enables manufacturers to create vehicle parts with specific color and resistance properties.
- Electronics Industry: In the electronics industry, masterbatch is used as a coloring material for parts like electronic device housings and cables.
- Medical and Pharmaceutical Industries: Masterbatches are used in the production of medical plastic items such as syringes, bottles, and pharmaceutical containers. Due to their specific properties, including antibacterial effects, they are very useful in these industries.
- Textile Industry: Masterbatches are also used in the production of synthetic fibers and colored textile products. They help manufacturers create durable and colored products.
Conclusion
Masterbatch is one of the most important materials in the plastics industry, enabling manufacturers to color plastics economically and with high quality. With features like uniform coloring, cost-effectiveness, and compatibility with various additives, masterbatch has a wide range of applications in many industries. Understanding the production process and types of masterbatch can help you make better decisions when choosing this material for your projects.